Effectively synthesizing a key raw material of the silicon chemical industry from silica
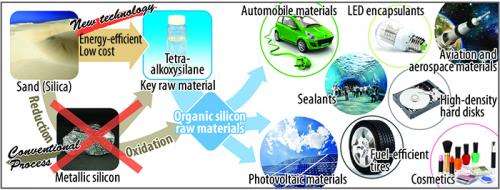
Researchers have developed a technology capable of efficiently synthesizing tetraalkoxysilane through a one-step reaction between alcohol and silica, the primary constituent of sand. Tetraalkoxysilane is a key raw material of the silicon chemical industry and a promising raw material for silicone and other various organic silicon materials.
From a chemical formula perspective, tetraalkoxysilane is produced by a reaction between silica and alcohol, with water being produced as a by-product. However, synthesizing tetraalkoxysilane by the reaction between silica and alcohol is difficult, because the reverse reaction, producing silica and alcohol from tetraalkoxysilane and water, is much more favorable. In the present research, the researchers discovered that tetraalkoxysilane could be obtained in one step by adding an organic dehydrating agent to the reaction system of silica and alcohol to remove the water by-product. Also, the efficiency of the reaction was further increased by performing it in the presence of carbon dioxide and catalysts, metal alkoxide and alkali metal hydride. This technology paves a new path to the energy-efficient, low-cost manufacture of organic silicon raw materials from sand.
The details of this technology will be presented at the third JACI/GSC Symposium held from May 22 to 23, 2014 at the Tokyo International Forum (Chiyoda, Tokyo).
Tetraalkoxysilane has utility as a raw material for high-purity synthetic silica and for protective films and insulating films used in electric devices. It is a promising raw material for various organic silicon materials, especially silicone, which is used in many different industries. Tetraalkoxysilane is industrially manufactured by the following methods. The starting material, natural silica stone (the main constituent of which is silica), is reacted with carbon at a high temperature by using a large amount of electrical energy to reduce the silica stone to metallic silicon. Metallic silicon is reacted with chlorine to form silicon tetrachloride, which is further reacted with alcohol. Alternatively, metallic silicon is directly reacted with alcohol. However, both methods are typical high-energy-consumption processes, because they involve a metallic silicon manufacturing step that requires high temperature. This fact is also one reason for the high cost of producing various silicon raw materials from metallic silicon such as tetraalkoxysilane.

Meanwhile, one known method for obtaining tetraalkoxysilane directly from silicon is reacting silica and dialkyl carbonate using a catalyst such as alkali metal hydride. This method does not use metallic silicon as a raw material, so it is advantageous from the perspective of energy efficiency. However, dialkyl carbonate, a relatively expensive compound, must be used at a minimum of twice the quantity of silica, which makes using this method to manufacture tetraalkoxysilane on an industrial scale very costly.
AIST focused on the method of directly reacting silica and alcohol to manufacture tetraalkoxysilane without using metallic silicon and discovered that tetraalkoxysilane could be efficiently synthesized by reacting silica and alcohol in the presence of an organic dehydrating agent, carbon dioxide, and a small quantity of catalysts.
From a chemical formula perspective, tetraalkoxysilane and water are produced when silica is reacted with alcohol (Fig. 1). While this reaction does produce some tetraalkoxysilane, it does not produce a good yield because tetraalkoxysilane and water react with each other to convert back to silica and alcohol. However, if the water produced in the reaction is consecutively removed from the reaction system, the reaction back to silica and alcohol is inhibited and a high yield of tetraalkoxysilane would be obtained (Fig. 1).
In this research, the researchers added an organic substance, acetone dimethyl acetal, as a dehydrating agent to the reaction of methanol and silica (purity: 99.7% or higher; particle size: 75-150 µm) and performed the reaction for 24 hours at a temperature of 242 °C to obtain an 18 % yield (based on silica) of tetraalkoxysilane (Fig. 2). The efficiency of the reaction was further increased by performing it in the presence of carbon dioxide and adding a small quantity of metal alkoxide and alkali metal hydride as catalysts. For example, a small quantity of titanium(IV) methoxide and potassium hydroxide were added when reacting silica, methanol, and acetone dimethyl acetal under carbon dioxide pressure (2 MPa), and after a reaction period of 24 hours, a 48 % yield was obtained. In addition, if the reaction period was extended to 96 hours, the yield reached 88 %. This is believed to be due to methanol reacting with carbon dioxide to become activated, causing it to react more efficiently with silica. Also, metal alkoxide is believed to promote the reaction between methanol and carbon dioxide. Meanwhile, alkali metal hydride acts to break down silica, i.e., it promotes the cleavage of the silicon-oxygen bond.

When reacted with water, acetone dimethyl acetal converts to acetone and methanol. However, acetone dimethyl acetal can be easily regenerated from acetone, so it can be re-used as a dehydrating agent. In addition, carbon dioxide only functions as a reaction promoting agent and is not consumed in the reaction; thus, it can also be re-used. Consequently, the only by-product of this entire reaction process is water. Also, the developed method is advantageous over conventional manufacturing methods that use silicon tetrachloride, because the developed method does not use chlorine compounds and thus does not carry the risk of chlorine contamination that exists in the conventional methods.
The developed technology allows tetraalkoxysilane, a key raw material in the silicon chemical industry, to be efficiently synthesized from the inexpensive and widely available raw materials, i.e., silica and alcohol. By avoiding the use of metallic silicon, this manufacturing process is energy-efficient and low-cost, so the use of organic silicon materials is expected to increase in the future.
The researchers intend to further increase the efficiency of this reaction by improving the structure of the organic dehydrating agent and the catalysts. In addition, they will verify the applicability of this reaction to various silicon sources and alcohols. In order to practicalize this technology in the next several years, the researchers will also investigate the regeneration of the organic dehydrating agent and the recycling of the catalysts and evaluate the cost advantage over the conventional tetraalkoxysilane manufacturing methods while also considering how to increase the scale of tetraalkoxysilane manufacturing.
Provided by Advanced Industrial Science and Technology