Mechanical response of nitinol to deformations gives insight into materials with targeted properties
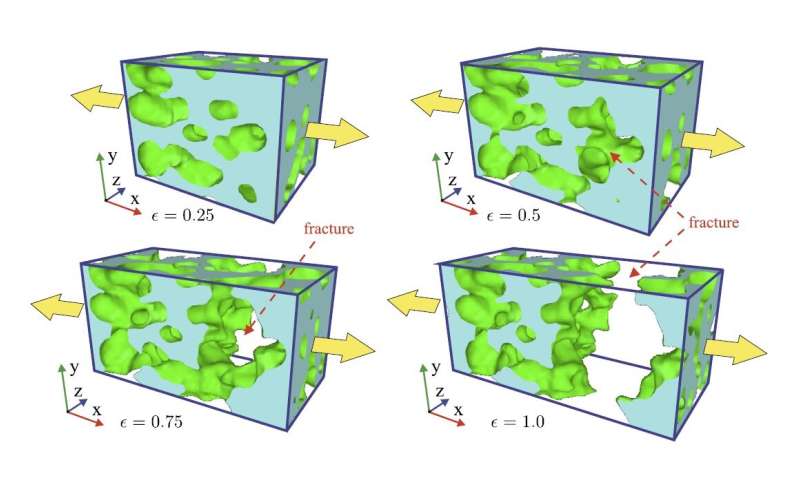
A paper by Kazan Federal University appeared in International Journal of Solids and Structures.
The work was sponsored by Russian Science Foundation; the project, headed by Professor Anatolii Mokshin, is titled "Theoretical, simulating and experimental research of physico-mechanical traits of amorphous-producing systems with heterogeneous local visco-elastic properties".
"We performed calculations for porous nitinol," shares first co-author, Associate Professor Bulat Galimzyanov. "It's widely used in various industries thanks to its unique physico-mechanical properties, such as low volume weight, high corrosion resistance, high biocompatibility and shape memory. Obtaining nitinol as amorphous foam is very labor-intensive, it requires high temperatures and extremely high melt cooling rate (over 1,000,000 K per second). Obviously, traditional experiments in this case are very costly and complex. We used computer modelling based on molecular dynamics."
As Galimzyanov explains, amorphous metallic foams are prospective materials.
"Their cell structure comprises a solid metallic frame with gas-filled pores. Pores can be either hermetic or conjoined. The volume ratio of pores and their hermeticity determine the primary physico-chemical properties of the metallic foam, among which are low heat conductivity, high plasticity, and good noise absorption. Thanks to that, metallic foams can find wide applications in the automotive industry, shipbuilding, and aerospace industry," says the interviewee.
As the research shows, amorphous porous nitinol can sustain major mechanical loads, significantly higher than crystalline nitinol.
Apart from the aforementioned applications, amorphous porous nitinol can also be used in prosthetics and biocompatible materials because it's much more resistant to stretching and shrinking than bones but has the same porousness.
More information:
Mechanical response of mesoporous amorphous NiTi alloy to external deformations
www.sciencedirect.com/science/ … ii/S0020768321001311
Provided by Kazan Federal University