Compact sensing technology measures mixture concentrations of three or more gases in real time
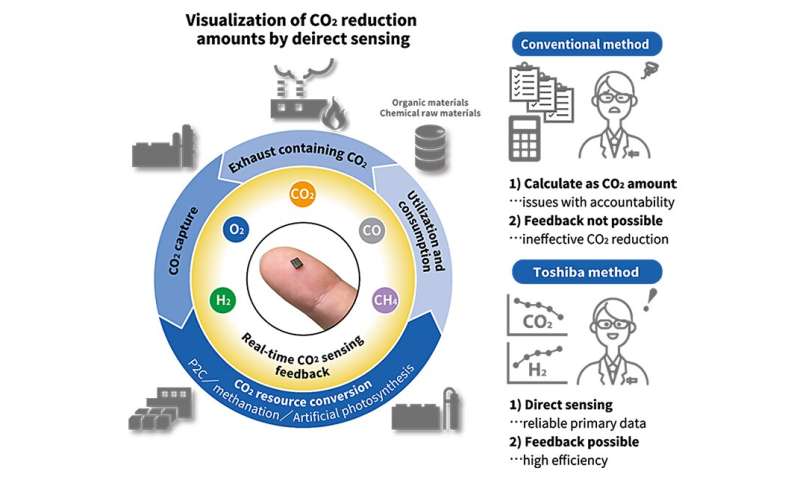
Researchers at the Toshiba Corporation have developed a world-first compact sensing technology that can simultaneously and rapidly measure gas concentrations in real-world environments, even for gas mixtures containing three or more gases, such as carbon dioxide (CO2), hydrogen (H2), and carbon monoxide (CO).
Compared with gas chromatography, the method conventionally used to measure gas concentrations, the developed system is less than 1/200th the size and operates more than 150 times faster. The miniaturization technology is based on micro-electromechanical systems (MEMS) technology, which uses microfabrication technologies to integrate electrical circuits and micromechanical components such as sensors and actuators on a single substrate.
Using proprietary MEMS technologies, the researchers have realized high-speed, compact, and simultaneous measurements of multiple gas concentrations by batch-forming ultra-small sensors with different sensitivities on a single substrate and using an algorithm to process each sensor's detection values. Using a prototype, the team demonstrated the effectiveness of this compact sensing technology under real-world environment with a mixture of gases including CO2, H2, and CO.
This technology enables real-time monitoring of concentrations of gases including CO2, H2, and CO in the mixture. It also contributes to improving the efficiency of technologies for converting CO2 into valuable gas resources, and furthermore enables direct measurements of the emissions of various greenhouse gases, which are currently calculated as CO2 equivalents, enabling the acquisition of highly reliable carbon footprint data.
The team presented the details of this technology on June 28 at TRANSDUCERS 2023, an international conference in the MEMS field, to be held in Kyoto from June 25 to 29.
Development background
To realize a carbon-neutral society, efforts are underway worldwide to develop CO2 resource conversion technologies that convert CO2 into valuable gas resources, as well as technologies to realize carbon footprint displays shown in terms of CO2 equivalents of greenhouse gas emissions throughout the entire life cycles of products and services, from raw material procurement to disposal and recycling.
CO2 conversion technologies include power-to-chemicals (P2C) technologies, which use electricity from renewable energy sources to convert CO2 into chemicals, and methanation technologies for synthesizing methane, the main component of natural gas, from CO2 and H2.
These technologies convert CO2 into resources by decomposing it through electrochemical reactions or by reacting it with other gases. To achieve highly efficient conversion of CO2 into resources, it is important to control optimal gas reaction conditions while performing real-time monitoring of the composition and concentration of the reacting gases. To achieve reliable carbon footprint, it is also necessary to measure and accurately visualize the concentrations of each greenhouse gas.
In actual environments, however, gas reaction processes generate byproduct gases and water vapor in addition to CO2 and generated resource gases, resulting in a mixture of several types of gases. Efficiently converting CO2 into a resource and accurately determining greenhouse gas concentrations requires accurate real-time measurements of the components and concentrations in the gas mixture (Figure 1).
An analytical instrument called a gas chromatograph is currently used to measure gas concentrations, but the time required for those measurements makes real-time monitoring difficult. Also, the large size of those devices requires the installation of complex systems in facilities that will perform P2C or methanation. Gas sensors are currently being developed worldwide for increased speed and reduced size. Of the three main methods for gas sensing—metal oxide semiconductors, catalytic combustion, and thermal conductivity—the thermal conductivity type is most effective from the standpoint of tolerance.
The gases generated by CO2 conversion technologies often contain gases with a strong poisoning effect such as CO, and metal oxide semiconductor and catalytic combustion methods have the issue of these poisoning causing changes in the gas reaction material. By contrast, thermal conductivity-based methods measure gas concentrations based on the fact that different gases have different heat transfer properties (thermal conductivity).
These methods are robust against gases with a strong poisoning effect because they do not employ a gas reaction material. However, when three or more gases are present, it has not been possible to determine which gas is transferring heat, meaning that concentrations could not be calculated.
Features of the technology
Against that background, Toshiba researchers have developed a technology for determining which gases are transferring heat by employing multiple thermal conductivity gas sensors with different sensitivities and using an algorithm to process the values detected at each sensor and outputting them as measurement values for each gas concentration.
This allows both robustness against gases with a strong poisoning effect and measurements of the concentrations of three or more gases in a mixture. This technology can be increasing the number of thermal conductivity gas sensors, thereby increasing the number of gases to be measured.
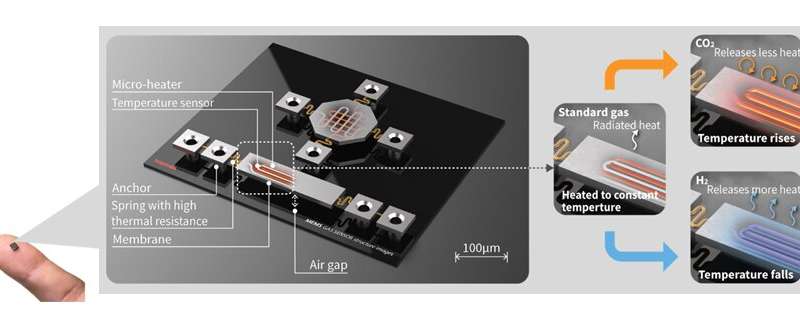
In addition, to increase measurement speed and reduce device size, the researchers adopted a MEMS technology by which electrical circuits and tiny mechanical components such as sensors and actuators can be integrated on a single substrate through microfabrication. They have developed a proprietary MEMS manufacturing platform technology that enables the batch fabrication of a variety of MEMS devices, achieving higher speeds and smaller sizes by fabricating multiple ultra-compact thermal conductivity gas sensors with different sensitivities on a single substrate (Figure 2).
With this technology, the compact thermal conductivity gas sensors were successfully used to measure the concentrations of each gas, even for mixtures containing three or more gases. This technology is also expected to increase the useful life of gas sensors, because no sensor poisoning due to adsorption occurs.
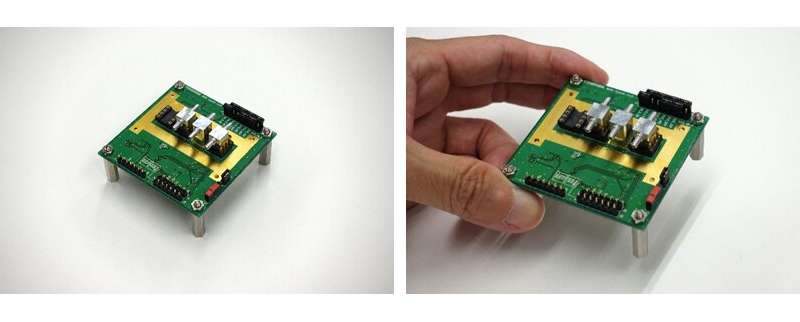
The researchers fabricated a prototype unit comprising thermal conductivity gas sensors batch-formed using MEMS technology, a nozzle for introducing gas, and a detection circuit (Figure 3). The prototype has a module size of approximately 106 cm3, less than 1/200th of the average size of a conventional gas chromatograph (approximately 22,740 cm3). A prototype CO2 electrolysis cell was attached as a real-world environment, and experiments were conducted to simultaneously measure the concentration of each gas in a humidified mixture of CO2, H2, and CO.
As a result, it was demonstrated that this technology can measure each of the three gas concentrations in 1.7 seconds, more than 150 times faster than the five minutes measurement time of a conventional gas chromatograph (Figure 4). This was a world-first measurement of three gas concentrations performed in real time and in a real-world environment.
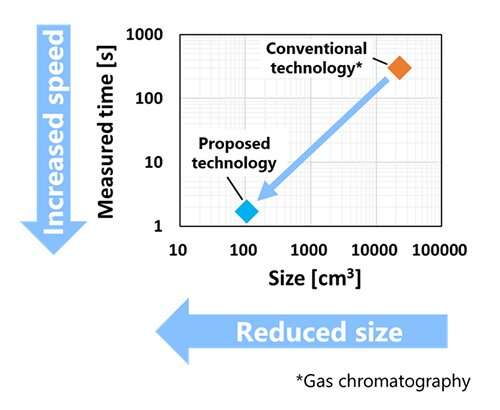
Toshiba will continue to optimize sensor structures and algorithms based on the knowledge obtained from this prototype, aiming for commercialization of this technology by 2026 through further demonstration tests.
This technology allows real-time monitoring of the concentrations of each gas in a mixture, contributing to the realization of a carbon-neutral society by improving the efficiency of CO2 resource conversion technologies and providing reliable carbon footprint data. This technology can also be applied to the sensing of individual gases to improve hydrogen leakage detection, indoor air-quality monitoring, and intestinal environment monitoring through exhaled hydrogen.
Provided by Toshiba Corporation News Releases