Research group designs dynamic materials for tomorrow's tech
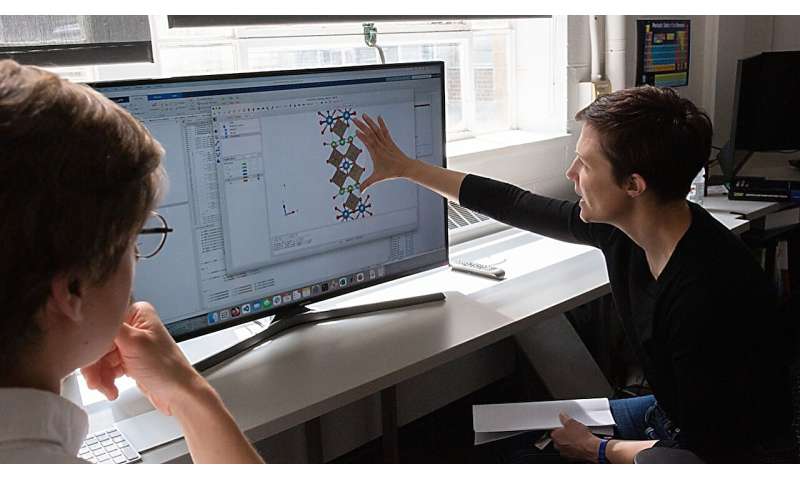
A Boeing 787 Dreamliner is among the fastest and most fuel efficient passenger planes in the world today. But for many passengers, the most amazing thing about the Dreamliner might be the windows. With the press of a button, passengers can change the window pane from clear to opaque, blocking light as if lowering a window shade. Flight attendants can also control the window's opacity, "lowering the shades" without needing to disturb passengers. A Dreamliner doesn't need pull-down shades because the optical properties of its windows change in response to an electrical current.
This is an example of a functional material—one with properties that change in response to an external stimulus. "Functional materials are the basis of so many useful, modern technologies," says Nicole Benedek, associate professor of materials science and engineering. "You find them in computer chips, in ultrasound machines, in solar panels; they are everywhere."
Benedek and her lab use theoretical and computational techniques to discover or design functional materials with certain target properties. "We provide materials candidates for particular applications," Benedek says. "You can't always anticipate exactly what properties will be needed in any given situation. Everything is made of something, so we try to provide as many horses for the race as possible."
Pushing a rare earth titanate over the edge
The Benedek Group focuses primarily on complex oxides, particularly a class of materials known as perovskites. Distinguished by a particular crystalline structure, perovskites can exhibit a range of interesting properties, including ferroelectricity, superconductivity, magnetism and piezoelectricity.
Recently, Benedek and her colleagues turned their attention to rare earth perovskite titanates. The molecules in these materials are made up of one titanium atom, three oxygen atoms and one atom of a rare earth element. Depending on which one of the 17 rare earth elements are involved, the single, unpaired electrons in the outer shell of the titanium atoms will either align their spin all in the same direction, known as ferromagnetism, or in a checkerboard pattern, known as G-type antiferromagnetism. If the spin of the outer shell electrons align, the material will be magnetic; if the spins form a checkboard pattern, the material as a whole will be nonmagnetic.
When looking at a phase diagram showing the electron spin for each of the rare earth perovskite titanates, a pronounced gap stands between the ferromagnetic and G-type antiferromagnetic materials, Benedek says. "There are no rare earth perovskite titanates that exist in that middle area," she says. "But in previous work, people speculated that if you could make a material that falls in the gap, it should be what's known as an A-type antiferromagnet. That is, it should exhibit what's often called 'layered ferromagnetism'—the spins on the titanium atoms align in one direction in one layer and then in the opposite direction in the next layer up."
Perched at the edge of that gap, on the ferromagnetic side, is the perovskite titanate made with the rare earth element gadolinium: gadolinium titanate (GdTiO3).
"We wondered whether we could push [gadolinium titanate] out of its typical ferromagnetic state, its equilibrium, and thereby into the gap. That is, into the A-type nonmagnetic part of the phase diagram," Benedek says. "It turns out we can, at least in theory. If you shine a light on gadolinium titanate in a special way, that turns off the magnetism. You can use that as an optical switch to turn the magnetism off and on."
Benedek's prediction is ready to be tested by materials engineers. Should the prediction hold true, gadolinium titanate might open the door for new approaches to data storage and a number of other technological innovations.
The mystery of negative thermal expansion
Most solid materials expand as they get hotter and shrink as they cool. Before computers, thermal expansion was the mechanism behind thermostats, and it's the reason that concrete road surfaces sometimes buckle in extreme temperatures if they are not properly engineered. Lead titanate (PbTiO3), however, is one of a few materials that exhibit negative thermal expansion—it actually shrinks as it gets hotter.
It's no secret among materials scientists that lead titanate exhibits negative thermal expansion, but the underlying reason for it has yet to be established. In a project with materials science and engineering graduate student Ethan T. Ritz, Ph.D., Benedek wanted to understand the underlying mechanics that contribute to lead titanate's negative thermal expansion. "There's still a lot we don't understand about how materials conduct heat at the atomic level," Benedek explains.
The project was supposed to be an easy warmup for Ritz before he tackled another, more complicated one. "There was a theory that the cause of negative thermal expansion in a material such as lead titanate involves a certain kind of lattice vibration," Benedek says, and that's what she and Ritz expected to demonstrate. Instead, Ritz came to Benedek with unexpected results showing that the lattice vibration commonly associated with negative thermal expansion in other materials was not observed in lead titanate.
"I told him, "This doesn't make sense. You're probably doing something wrong,'" Benedek remembers. "He said, 'No, you're actually wrong. And this is why.'"
With further investigation, the researchers discovered the negative thermal expansion in lead titanate was a product of the unexpected interplay between vibrational and elastic properties. "Ethan did just what you want a student to do," Benedek says. "You want them to tell you when you're wrong and keep persisting, which is just what he did."
Explaining the unexplainable
Benedek develops theoretical frameworks that allow her to explain the results of other researchers' experiments. This comes into play, for instance, when a materials engineer makes a new material that exhibits properties that can't be explained with current theories.
In the best of all worlds, she likes to endow her frameworks with the ability to predict how an as-yet unfabricated material will behave, as well as to explain why a realized material behaves the way it does. Benedek is pursuing just such a framework in a series of ongoing collaborations with synthetic chemist Michael Hayward at Oxford University. Their work takes up new materials in the perovskite family known as Dion-Jacobson phases.
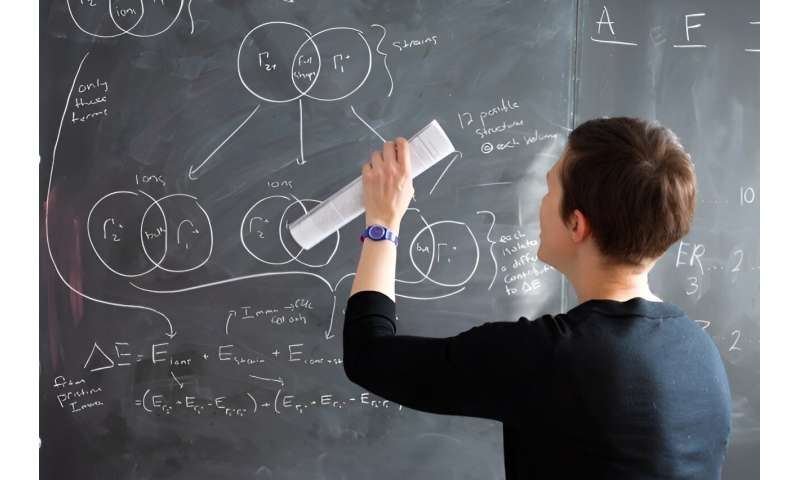
"People had overlooked these materials in the past because they thought they didn't do much," she says. But Benedek took a closer look and predicted that certain Dion-Jacobson phases ought to be ferroelectric, meaning that they would have a spontaneous polarization that could be reversed by applying an electric field. Ferroelectric materials are used for storing electrical charges in capacitors, among other things, she explains. The ferroelectric dipole moment can also be used to store information—for example, in computer memory cells.
After working out some calculations and developing theories based on a series of Dion-Jacobson phases, Benedek concluded that they held many more polar materials than generally thought.
Soon after that, she happened to meet Hayward at a conference. "Mike makes those kinds of complex oxide materials," she says. "So he went back to his lab and made the ones I had theorized about. It turned out they were polar, but there was a little twist: they had a different structure than I predicted."
Benedek refined her theory based on Hayward's findings. Using what they had learned, Benedek and Hayward looked at other potential candidates for ferroelectric Dion-Jacobson phases. In the end, Hayward synthesized eight distinct materials. "Some were completely new," Benedek says. "Some were materials that others had made before but then put aside because they didn't see any interesting properties. Mike made those materials again and did very careful measurements, and he found that they actually were polar.
"Our collaboration has been really successful," she continues. "We've made new materials, but we've also learned some very fundamental solid-state chemistry about them at the same time."
The reason behind it all
Benedek always wanted to be a scientist as a child but had no idea that materials science even existed. Initially, she settled on a career in medical research, or medical science as it's known in Australia, where she grew up.
"I was going to cure cancer," she laughs. "There was a lot of biochemistry and molecular biology in that degree field. Those are very complex disciplines, and I found myself always wanting to know things at a more fundamental level. I could see what was happening, but why was it happening?"
Eventually she found her home in materials science. "It's inherently a very interdisciplinary area of research," she says. "A really nice combination of chemistry, physics, engineering, biology, too, depending on which area you're working in. That's how I ended up here. I like chemistry. I like physics. I like it best when I'm doing them together. And that's materials science."
Provided by Cornell University