Investigating hops as a circular building material
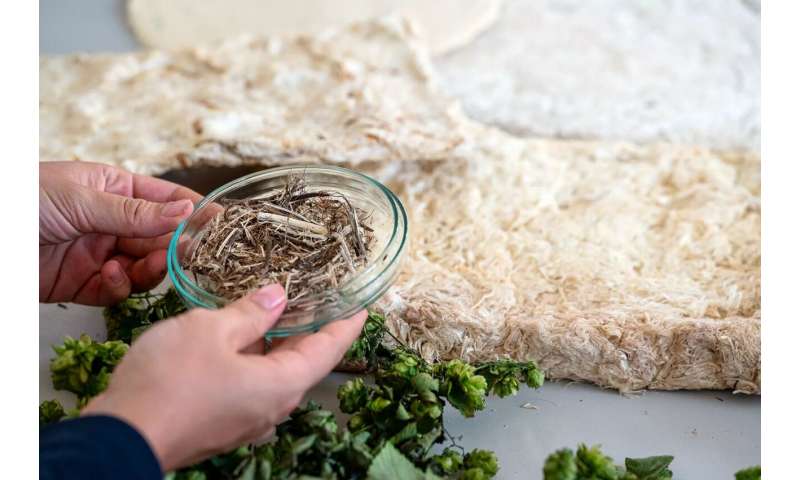
The construction industry consumes enormous resources and is responsible for a large proportion of global CO2 emissions. The team of HopfON wants to address this situation. Their vision is to produce recyclable, climate-friendly building materials using agricultural waste and resources.
The idea came to them while enjoying a beer in their student residence. Thomas Rojas Sonderegger, a student in construction engineering back then, was telling architecture student Marlene Stechl about a talk he had attended. It was about a Colombian who was producing construction materials with banana fiber.
"So we thought it would be great if we could make our own locally sourced building material. This could save greenhouse gas emissions," says Stechl. "We thought about which solution might work in Bavaria. We were actually joking when we said, It would be cool to use hops. The next day we actually started to do some research."
A promising fiber-based material
The two students soon learned that hops stem from the same plant family as hemp, which has become increasingly important as a building material in recent years. "We started gathering more information about this plant—and what actually happens to the waste material from hop cultivation," says Stechl. In architecture and design professor Niklas Fanelsa, they found a supporter who not only contributes his scientific expertise, but also gives the team access to the Bioregional Design Lab at TUM and thus enables further material tests.
Because only a small percentage of the hop harvest is used for beer production, Stechl and Sonderegger came up with the idea of using also waste from hop farmers. "Along with the ecological benefits, this also saves costs," says Stechl.
The fibrous structure of hop plant lends tensile strength to the material, making it especially suitable for acoustic panels, insulation and structural boards. The woody cores of hops, known as shives, provide the material with additional compressive strength. Like hemp, hops also have good heat insulation characteristics. To validate the team's chosen material, Stechl tested the flammability of the hop plant as part of her master's thesis and found no cause for concern.
Excellent idea
With their idea, Stechl and Sonderegger took part in the Urban Prototyping Lab of the TUM Chair of Architectural Informatics. Participants were invited to propose solutions to problems from the construction industry. After submitting their detailed concept, they were invited to apply for the 2022 TUM IDEAward. They won first prize, which came with 15,000 euros in start-up capital.
The TUM IDEAward attracted the attention of business student Mauricio Fleischer Acuña, who soon joined the HopfON founding team. He was followed in 2023 by Matthias Steiger, a biochemist working on a doctorate at the Chair of Chemistry of Biogenic Resources, who is now developing further prototypes for HopfON. HopfON also received the TUM Booster Grant, which includes one year of funding worth 45,000 euros, and two prototyping grants from UnternehmerTUM, the Center for Innovation and Business Creation. The support through the ecosystem of TUM is of such great help, especially when it comes to ramp up operations and founding the company in 2024, as Acuña explains. Another key pillar is the location: The world's largest hop growing region, Hallertau, is on Munich's doorstep.
Logistical challenges in the hop harvest
The hop harvest in Hallertau in September 2023 proved to be a big challenge for the HopON team. "We didn't have a clue about containers, trucking companies or drying sheds," said Stechl. "First we had to familiarize ourselves with the entire logistics chain. That was true experimental work for us." For example, we had to figure out the best way to separate the hops from the horizontal wires that the plants are trained along.
In their first harvest the founders got a lot of support from the farmers they worked with. Harvesting the plants for HopfON was also new territory for them. But they were happy to get involved. "It was just great. I had the feeling that you can count on an amazing response if you have a vision and share it," says Stechl. With this energetic and creative support, the team was finally able to get a process up and running to secure enough raw material for production in the upcoming year. This was crucial, explains Acuña, as the hop harvest takes place only once a year.
A recyclable product
It is important to the founders to offer a recyclable product. For that reason, they completely avoid using artificial or non-soluble additives. That means that the hop-based construction materials can be broken down into their original components after use and reconstituted as new products. This is a key unique selling proposition as compared to other sustainable materials, says Acuña. It is also an essential prerequisite for the market launch, which is planned for 2024 with the rollout of acoustic panels for soundproofing applications.
The biggest challenge at the moment? Just to keep everything going—because some of the founders have full-time jobs alongside their HopfON roles. But their goal is a big motivator, says Stechl. "We're working towards the day when we can offer a serious alternative to conventional construction materials."
Provided by Technical University Munich