New microstructural imaging system ready for global use
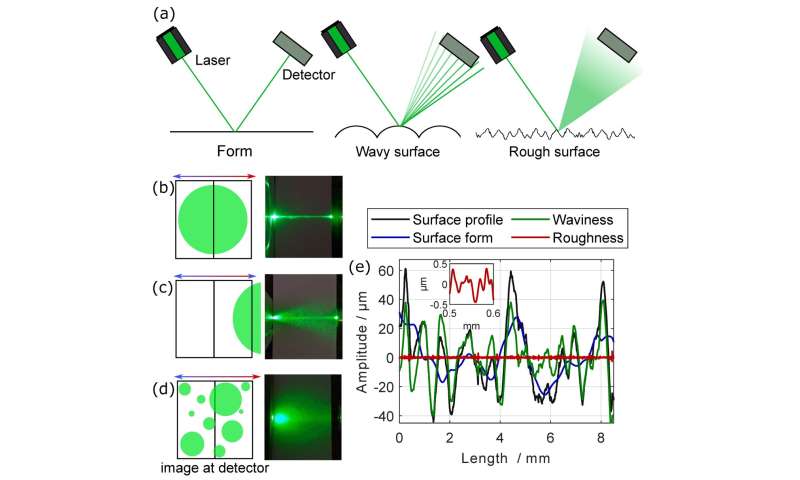
A microscopy technique invented at the University of Nottingham that can image the microscopic elasticity of engineering materials is set for global use after being adopted by the U.S. company Coherent Photon Imaging (CPI). The underlying research is published in the journal Applied Sciences.
Many materials are made up of thousands of small crystals. The size, shape, and stiffness of these are essential to the material's performance. In real engineering materials, such as aero engine components, the stiffness of these crystals previously hasn't been able to be measured, but could only be identified from specially prepared single crystals, which had to be prepared in laboratories at great expense.
These single crystals often had significantly different properties from the real engineering material they were supposed to represent due to differences in their preparation. This meant that it was previously impossible to determine the fundamental microscopic stiffness of real materials—an issue industry has faced for more than 100 years.
Now, the university's patented invention, SRAS, and the newly patented SRAS++ technique, can measure this complex stiffness in real materials and "image" the stiffness, making it possible to map variations, for the first time. These brand-new discoveries pave the way for a myriad of other applications, such as the detection of residual stress and in situ monitoring the progress of processes such as heat treatment and annealing.
The technology has already started to be used in aerospace to evaluate the structural integrity of materials used in the manufacture of critical engine components. Now, it's set for global adoption through a collaboration with Iowa-based CPI.
"Previously, the only way to measure the elasticity matrix of a material was to cut it up or attempt to grow a single crystal of the material, a process that cannot be done for many materials, such as the titanium alloys used in modern jet engines, which wastes money, time, and materials," says Professor Matt Clark, co-lead on the study from the Optics and Photonics Research Group at the University of Nottingham.
"We're thrilled to be able to announce our partnership with the team at CPI, marking a significant step in the wider commercialization of SRAS and SRAS++. Clients are already signing on the dotted line to adopt the technology and we look forward to seeing our research turn into reality," says Clark.
Recognizing both the elegance of the SRAS and SRAS++ methods, as well as their potential to be widely adopted, established a partnership to commercialize the technology.
Pete Collins, Founder and Co-owner of CPI, says, "Rarely does a new measurement technique emerge that has the potential to truly transform the way that industry operates when it comes to materials characterization, design, and qualification. Considering the advancements over the past 90 years, I assess that SRAS and SRAS++ are equivalently significant advances as the transmission electron microscope, scanning electron microscope, focused ion-beam microscope, and the local electrode atoms probe.
"What sets this apart is that it measures not only a material's state, but also its elasticity, a capability none of these other methods can do. This is a game changer. We are delighted to be working closely with such a pioneering group to bring this technology to market as widely as we can," says Collins.
Dr. Richard Smith, associate professor and member of the Optics and Photonics Research Group, says, "We're continuing to look at other ways we can use SRAS and SRAS++ and have already incorporated it into 3D printing technology, creating a way to monitor the state of a material while it is printed. This is just the beginning for technology of this kind and we're excited to see how far our research can take us."
More information:
Wenqi Li et al, Imaging Microstructure on Optically Rough Surfaces Using Spatially Resolved Acoustic Spectroscopy, Applied Sciences (2023). DOI: 10.3390/app13063424
Provided by University of Nottingham